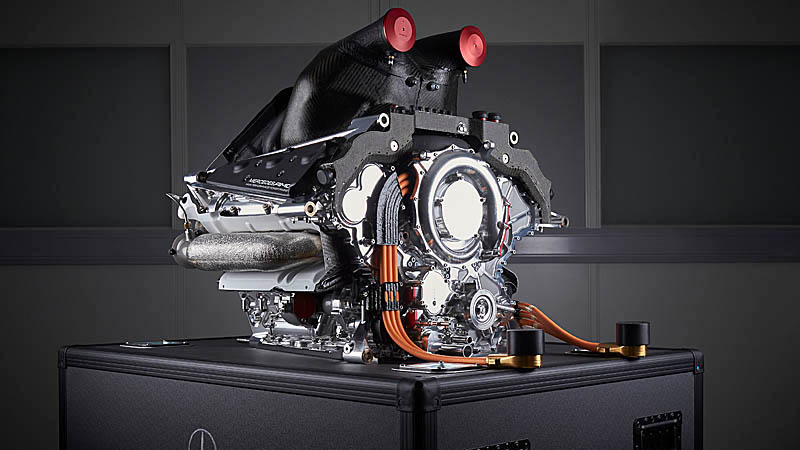
In 2014, Formula 1 switched away from V8 engines, electing instead to mandate all teams race with turbocharged V6 engines of 1.6 litres displacement, fitted with advanced energy recovery systems. The aim was to return Formula 1 to having some vague notion of relevance to modern road car technologies, with a strong focus on efficiency. This was achieved by mandating maximum fuel consumption for races, as well as placing a heavy emphasis on hybrid technology.
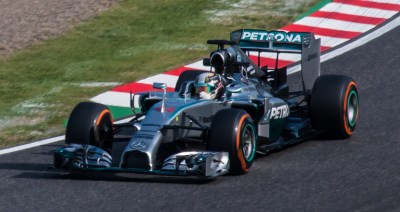
Since then, Mercedes have dominated the field in what is now known as the turbo-hybrid era. The German team has taken home every drivers and constructors championship since, often taking home the crown well before the season is over. Much has been made of the team’s engine as a key part of this dominance, widely considered to be more powerful and efficient than the competition at all but a few select races in the last seven years, and much of the credit goes to the company’s innovative split-turbo system. Today, we’ll explore why the innovation was such a game changer in Formula 1.
Many and Varied Gains
This article assumes a basic working knowledge of turbochargers. If you’re not quite up to speed yet, check out our primer on the topic!
The basic template given to the teams was to produce 1.6 litre engines with forced induction, with the option of using a turbocharger or supercharger, with all teams electing to use turbos in their designs. Additionally, teams were able to use energy recovery systems to further boost performance and efficiency. The MGU-K, standing for Motor Generator Unit – Kinetic, is connected to the engine’s crankshaft, harvesting energy under braking and supplying power during acceleration. The MGU-H, or Motor Generator Unit – Heat, is connected to the turbocharger’s shaft, and can thus turn waste energy from the exhaust into electricity, or conversely, spin up the turbocharger to reduce turbo lag.
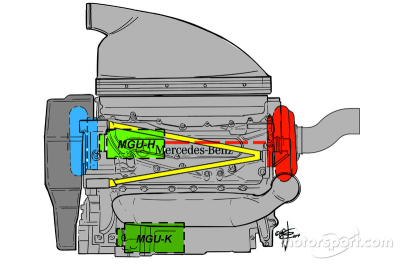
Most manufacturers went with tightly-packaged designs featuring relatively conventional turbos, albeit with a MGU-H unit attached for energy recovery. However, Mercedes decided to aim for an unconventional split-turbo design. In a regular turbocharger, the compressor wheel and turbine wheel are connected by a short shaft, with the respective housings mounted directly back to back. However, Mercedes realised there were a multitude of gains to be had by instead splitting the two halves further apart. Instead, the compressor was mounted at the front of the engine, and the turbine at the rear. The two were joined with a much longer shaft than is usual, passing through the vee of the engine. This also allowed the MGU-H to be mounted in the center of the vee, between the compressor and turbine.
The design promised a multitude of benefits. Separating the turbine from the compressor meant that heat from the exhaust gases wouldn’t bleed into the compressor as much, reducing intake temperatures and allowing the team to fit a smaller intercooler. The packaging benefits also allowed the team to make the whole engine, or power unit, more compact, giving the chassis designers more freedom to make aerodynamic optimisations to the car. It also allowed for cleaner, more straightforward routing of the exhaust piping, which helps with power output, and shorter intake piping, which helps reduce lag for better driveability.
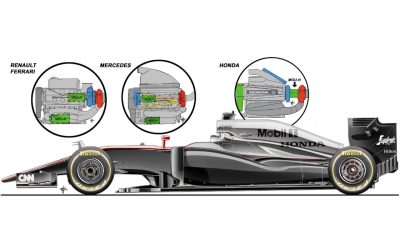
With all the benefits to be had, it raises the question why the solution was such a novel one, and the reason is speed. The turbochargers in an F1 car spin at over 100,000 RPM. At such high rates of angular velocity, the slightest imbalance in a shaft can destroy a turbo in seconds. Making that shaft almost an order of magnitude longer only makes things worse, due to the greater moment arm created by the length exacerbating even the smallest vibrations significantly. However, top tier motorsport is the right venue for attempting new feats in materials and machining, and Mercedes were able to make the system work. The team leaned on their institutional experience with turbocharging in the Daimler truck division, with work on the engine beginning as far back as 2011 to prepare for the initial 2014 season. After their dominating performance in the first three years of the turbo-hybrid era, Honda elected to copy the idea for their 2017 engine. More recently, Renault have been linked with a switch to the layout, with Ferrari rumoured to be considering the concept too.
Not Destined for the Open Road
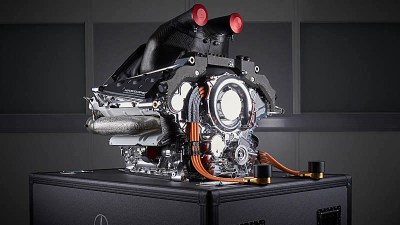
Despite Formula 1’s renewed focus on technologies that are transferable to the road, it’s not likely that you’ll see split turbos nestled in the vee of your performance road car any time soon. Formula 1 is a world where incremental percentage gains can make or break a World Championship effort, and where every last scrap of aerodynamic downforce is necessary to come out on top of the competition. Road cars simply don’t have any real reason to focus on such tight packaging, or minor gains in cooler inlet temperatures from such technology. It’s generally far simpler to bolt on a larger intercooler and make the bonnet a little longer instead. Additionally, the tight machining tolerances required for such a long, high-speed shaft would make such turbos prohibitively expensive for any road car. They’d also likely have maintenance intervals entirely unsuitable outside of the racing environment.
While split-turbo technology remains limited to on-track action in F1, it nonetheless shows how thinking outside the box and ignoring convention can lead to real world engineering benefits. While its competitors play catch up, we’re sure Mercedes F1 engineers are already looking around the corner for the next nifty idea that will end up worth a second a lap on the circuit.
Recent Comments